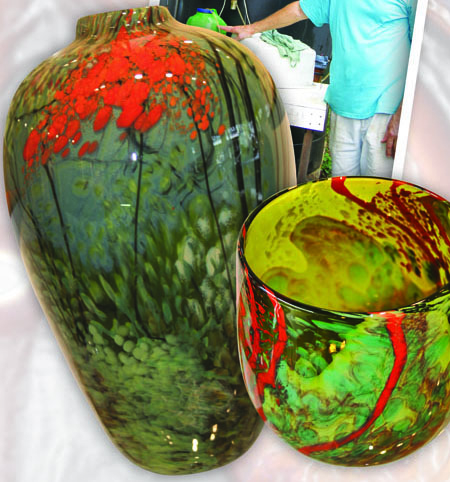
Used Veggie Oil Fuels Fabulous Glass Art
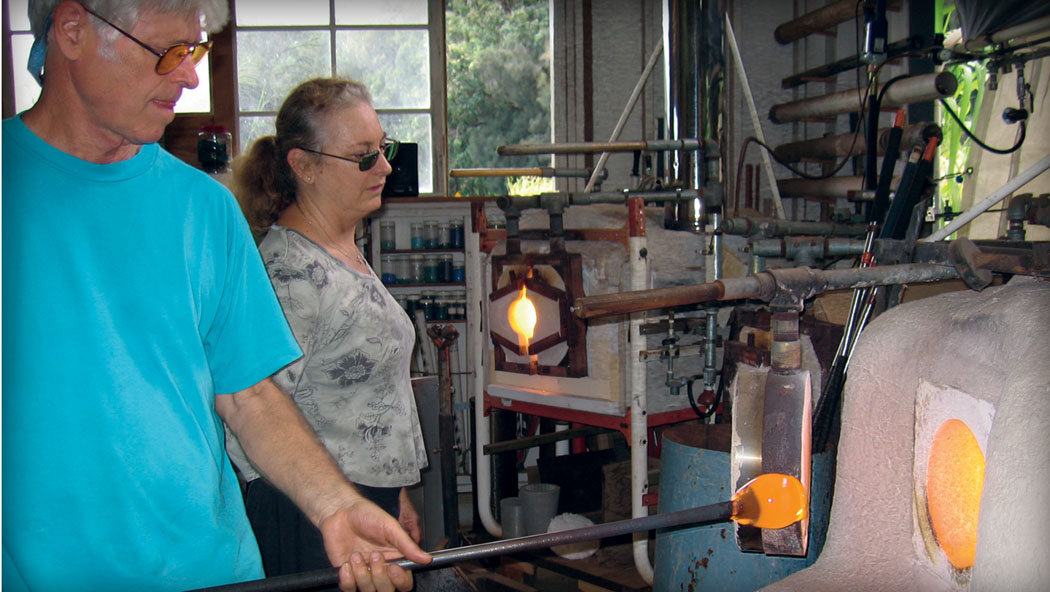
By Andrea Dean and Karen Valentine
In their studio on the Hamakua Coast, glass blowing artists Hugh Jenkins and Stephanie Ross move around each other in an intricate dance done with hot glass on the end of metal pipes. They pull clear glass from the crucible, turn it, add color, fusing it together, layer by layer, all the while blowing it into colorful, sculptural bowls and vases.
This is one hot art form! Glass blowing takes pellets called “batch” and turns them into glass pieces by melting them in a furnace at 2300° Fahrenheit. Beautiful art is created along the way, beginning with visions, reflections, drawings and color chemistry, then applying muscle and lung power while “painting” and sculpting with this medium that is first fluid and then fragile. Teamwork comes into play with Stephanie, the colorist whose background includes printmaking and fiber art, and Hugh, who began as a chemistry, oceanography and biology major, then “stumbled into glass blowing by hanging out with the wrong crowd,” he says.
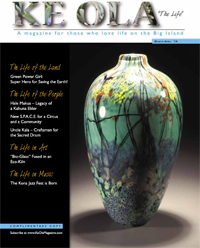
A knowledge of chemistry is helpful in many different art forms. And in Jenkins’ case, there’s physics, economics and environmental science, as well. One doesn’t normally think of art as being a field of endeavor that consumes a lot of energy or contributes to global warming, either, but it takes a tremendous amount of heat to melt glass and fire ceramics. When propane costs went from $1.40 to $4.95 per gallon, Hugh and Stephanie were faced with an energy crisis. They realized that they would not be able to continue as glass blowers with a propane bill of $5,000 a month. Necessity is the mother of invention and Hugh got busy. He started with inventing a heat recuperation system for the furnace that reduced their fuel consumption by 70 percent.
Committed to an environmental ethic, Hugh wanted to further reduce their reliance upon propane and use an available, local fuel source. Bring in the french fry grease! Jenkins began experimenting with running the furnace on used, straight vegetable oil (SVO) collected from local restaurants. After much trial and error, Hugh perfected the system last year. It may sound easy, but there are no instruction manuals or parts for a veggie oil glass furnace with a heat recuperation system. Hugh created his own burner system and hand fabricated many of the parts.
“Lowering our costs using heat recuperation and veggie oil has made the difference between survival and being able to do the kinds of things we want to do. We can be more artistic and not worry so much about sales,” he said.
Jenkins, who taught glass blowing and metal work at Punahou School on Oahu for 26 years, first saw an pportunity to fuel the glass blowing program at Punahou with malasada oil. He helped the school build a small furnace for melting glass colors which runs on the 180 gallons of malasada oil that is left over each year from the malasada booth at the Punahou Carnival. He’s become something of an authority on glass kiln design. His article entitled “Bioglass, Green Studios Benefitting Artists and the Environment,” appeared in the Glass Art Society Journal.
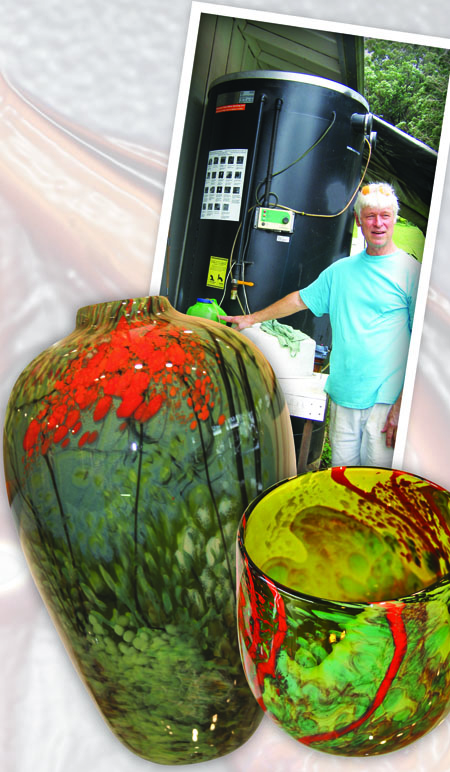
Ross, who earned her degrees first at California College of Arts and Crafts in Oakland, and then received her graduate degrees from the University of Hawai’i, Manoa, taught art in high school and elementary school. She was introduced to glass in1995 and has worked in collaboration with Hugh Jenkins since 1996. In 1999, the couple moved to the Hamakua Coast, where they found a house and studio combination that fit their working-artist lifestyle perfectly.
As a team, Jenkins and Ross have evolved their glass art over the past few years. Hugh admits that he was at first “very technical and tight about my forms. I insisted on symmetry in creating the bowl and vessel shapes.” Now they are moving into more natural shapes, in synch with the reflections of nature that they have incorporated into the colors and decoration styles of their pieces.
“We’ve decided to loosen it up,” Jenkins says. “Looking at shapes like stones, you see they take softer, more gentle forms. How did nature create them? How do they relate to each other? Rocks come in groups and we’re thinking of creating glass arrangements and selling them in groups. We want to feel like they’re part of their environment and reflect what’s around them, too.”
The colors seen in Jenkins and Ross’ glass pieces are obviously reflections of nature. In an impressionistic sense, the reds and blacks remind you of volcanoes, while frothy blues and white are very ocean-like, and multi-colored dots arranged among darker stripes remind you of flowers and trees.
As word has spread about Hugh’s eco-furnace, he has gotten inquiries from other artists with high gas bills and an environmental bent. But veggie oil isn’t for everyone, he cautions. “Picking shrimp tails and pieces of malasadas out of your fuel before you can use it is a bit messy.” Not to mention the fact that vegetable oil attracts critters that want to eat it, spoils quickly and gets gummy, kind of like the salad dressing that drips on the outside of the bottle. Additional time must be spent in continuous filtration and keeping the lines clean. Jenkins had to design the burners for the fuel, as they have much smaller orifices than those used in vehicles and industry. Fortunately, they no longer have to go around to restaurants and collect the oil, as now there are businesses that deliver it to them.
“Propane is a beautiful fuel,” he says. “But if we weren’t on vegetable oil, we wouldn’t be blowing glass.” The kiln takes several days to heat up to the right temperature and cool down when it’s finished, so the couple works daily during periods of four to five months each. That’s also a deterrent to part-time glass blowers.
North Kohala-based artist Peter Kowalke, whose company Art In Sight has a focus on fine art and ecology education, had been delaying building his kiln because of the disconnect between burning fossil fuels while teaching children about ecology. Hugh re-designed the kiln with a super efficient heat recovery system and in March 2008, he and Peter led a kiln-building workshop. What emerged was the 36-cubic-ft. “Mana Mama” community kiln. The kiln is currently being tested on propane and will be converted to veggie oil in the future. ❖
Jenkins’ and Ross’ glass art may be found in Honoka‘a at Big Island Glass, as well as Volcano Art Center, Kailua Village Artists’ Co-op, Pura Vida Gallery in Kapa‘au, Isaacs Center and Wishard Gallery in Waimea. Visit their website at www.bigislandglass.com.
They are planning an exhibition at the Volcano Art Center during August, 2010.